
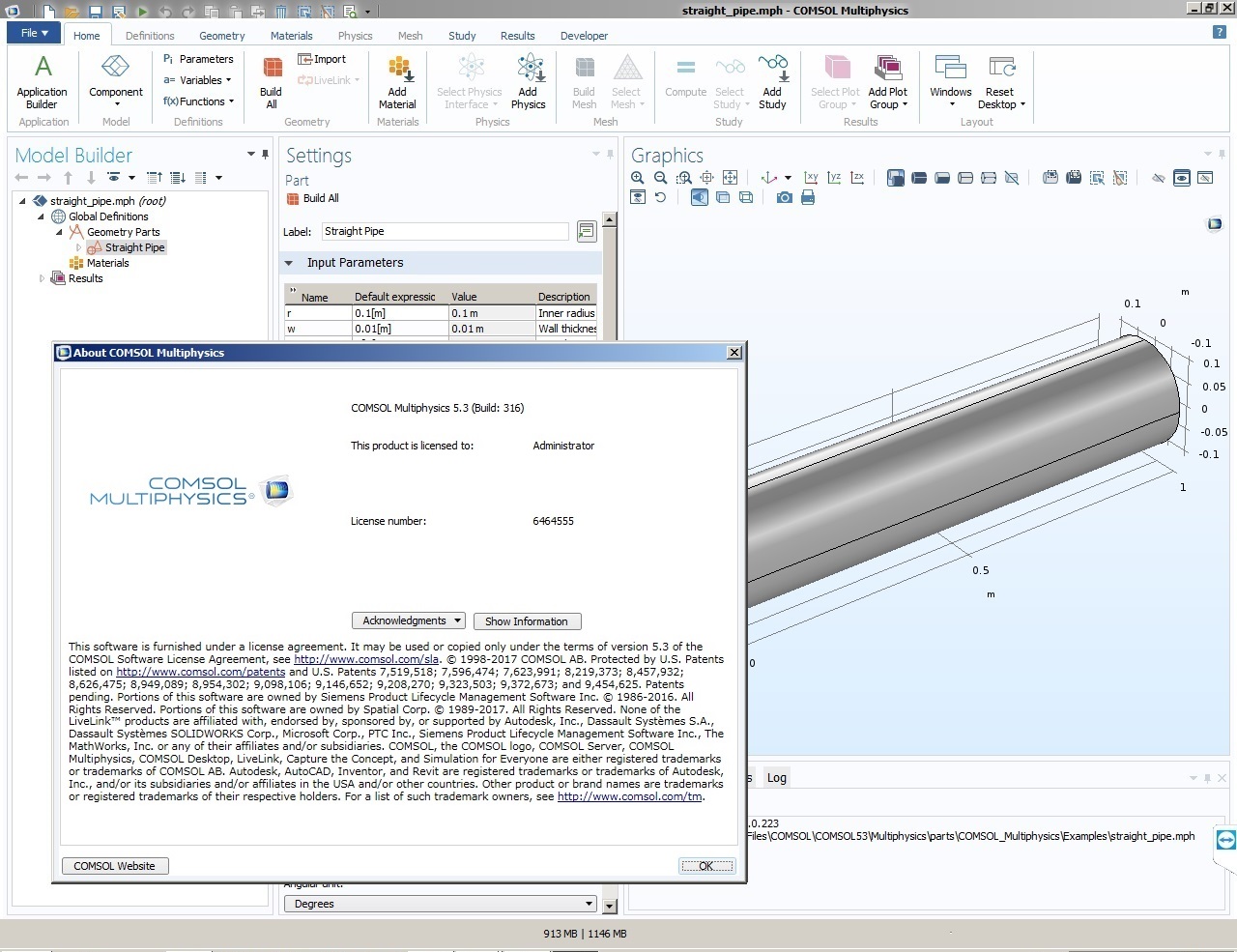
Surface differential probes are commonly used in the form of an optimized reflection differential split-D configuration, which has a relatively small footprint because of the shape and stacking of its receiver coils. Besides being virtually insensitive to gradual variations in the material’s thickness, conductivity, and permeability, the reflection differential probes compensate for the unwanted effects of the probe’s tilt or lift-off. These probe types are frequently employed to detect short and shallow surface breakings. Reflection differential and bridge differential probes have more elaborated designs. Low-frequency absolute surface probes (no more than 500 kHz) with relatively large footprint diameters are best suited to either evaluate thickness, permeability and conductivity of the components or detect near-surface defects and inhomogeneities since their lower operating frequencies imply higher penetration depths inside the material. They may possess different shapes and sizes depending on the type of application. Ībsolute surface probes, with their simplest configuration (a single multi-turn circular coil), are typically conceived to operate at a frequency range of 100 Hz to 4 MHz. In the aerospace industry, ECT is well-known for its superior inspection performance of bolt holes, lap joints, wheels and engine components. This wide diversity of applications has demanded the development of different configurations for eddy current (EC) sensors tailored to specific inspection purposes. Recent signs of progress in ECT is readily found in thickness measurement of coatings or thin conductive sheet metals, evaluation of conductivity and permeability variations, detection of surface and near-surface breakings such as cracks. Eddy current testing (ECT) has been routinely employed in various industries as a well-established NDT technique applied to conductive materials. Depending on the nature and location of these flaws, proper NDT techniques should be assigned for in-service inspections. A wide variety of fatigue-induced flaws may exist in the aircraft components, which requires having periodical inspections in place.

As an instance, aerospace industry, among all the industries that employ NDT to assess the integrity of structures, is tightly connected to human safety. In-service non-destructive testing (NDT) of components and systems is crucial when these systems are directly related to human safety. These defects may deleteriously affect the performance of components and industrial systems by reducing their expected lifetime.
Crack comsol 5.3 crack#
For instance, the fatigue crack is a very common defect type that could be frequently found in components under cyclic loads. Under specific loading and environmental conditions, these imperfections may grow and form critical discontinuities.
Crack comsol 5.3 free#
The materials’ structure in manufactured parts is almost never free of microscopic imperfections. The simulation results, generated by Comsol Multiphysics FEM package (COMSOL I, COMSOL multiphysics reference manual, version 5.3, COMSOL AB, 2018, for the cases of absolute and differential probes are checked for their extent of validity. This study shows that the simulation results on a commercial reflection differential split-D surface pencil probe closely estimate the experimental measurements of the probe’s impedance variations as it scans three EDM notches having different depths in aluminum. Parameters contributing to reliable FEM simulation results, such as maximum mesh size, mesh distribution, the extent of the surrounding air domain and conductivity of the air are investigated for the 3-D modelling of both absolute and differential probes. The outcome generated through the simulated scan of this absolute coil over a surface notch in aluminum is validated with existing experimental impedance data taken from the literature. In order to attain a better insight into the correct setup of the FEM parameters, a simple multi-turn cylindrical absolute coil has also been modelled. In this paper finite element modelling (FEM) has been employed to simulate the interaction of a reflection differential split-D probe with surface electrical discharge machined (EDM) notches in 3-dimensional (3-D) half-space. In recent years, a growing number of research works on their numerical modelling was conducted since the development of analytical or semi-analytical models for such a sensor may be prone to intractable complications. Differential eddy current probes are commonly used to detect shallow surface cracks in conductive materials.
